ส่วนที่ 1: เกียร์และ ชิ้นส่วนช่วงล่างรถยนต์
1. กระบวนการตัดเฉือนเกียร์
ตามข้อกำหนดโครงสร้างที่แตกต่างกัน กระบวนการทางเทคโนโลยีหลักของการประมวลผลชิ้นส่วนเกียร์คือการปลอมช่องว่าง → การทำให้เป็นมาตรฐาน → การตัดเฉือนการตกแต่ง → การสร้างเฟือง → การลบมุม → การตัดเฟือง → การโกน → (การเชื่อม) → การอบชุบด้วยความร้อน → การเจียร → การตัดแต่งตาข่าย
โดยทั่วไปแล้วฟันจะไม่ผ่านการกลึงหลังจากความร้อน ยกเว้นฟันหลักและฟันรองหรือส่วนที่ลูกค้าต้องการบดฟัน
2. การไหลของกระบวนการเพลา
เพลาอินพุต: การตีเหล็กแท่ง → การทำให้เป็นมาตรฐาน → การตัดเฉือนขั้นสุดท้าย → การกลิ้งฟัน → การเจาะ → การขึ้นรูปฟัน → การลบมุม → การตัดเฟือง → การโกน → การอบชุบด้วยความร้อน → การบด → การตัดแต่งตาข่าย
เพลาส่งออก: การตีเหล็กแท่ง→การทำให้เป็นมาตรฐาน→การกลึงให้เสร็จ→การบดและการกลึง→การโกน→การอบชุบด้วยความร้อน→การบด→การตัดแต่งการจับคู่
3. โฟลว์กระบวนการเฉพาะ
(1) การตีเหล็กแท่ง
การตีขึ้นรูปด้วยความร้อนเป็นกระบวนการตีขึ้นรูปเปล่าที่ใช้กันอย่างแพร่หลายสำหรับชิ้นส่วนเกียร์ยานยนต์ ในอดีตมีการใช้ช่องว่างการรีดร้อนและการรีดเย็นกันอย่างแพร่หลาย ในช่วงไม่กี่ปีที่ผ่านมา เทคโนโลยีการกลิ้งลิ่มแบบไขว้ได้รับการส่งเสริมอย่างกว้างขวางในการประมวลผลเพลา เทคโนโลยีนี้เหมาะอย่างยิ่งสำหรับการทำช่องว่างสำหรับเพลาขั้นบันไดที่ซับซ้อน ไม่เพียงแต่มีค่าความเที่ยงตรงสูง ค่าเผื่อหลังการประมวลผลเพียงเล็กน้อย แต่ยังให้ประสิทธิภาพการผลิตสูงอีกด้วย
(2) การทำให้เป็นปกติ
วัตถุประสงค์ของกระบวนการนี้คือเพื่อให้ได้ความแข็งที่เหมาะสมสำหรับการตัดเกียร์ที่ตามมา และเพื่อเตรียมโครงสร้างสำหรับการอบชุบด้วยความร้อนขั้นสุดท้าย เพื่อลดการเสียรูปของการอบชุบด้วยความร้อนอย่างมีประสิทธิภาพ การทำให้เป็นมาตรฐานทั่วไปได้รับผลกระทบอย่างมากจากบุคลากร อุปกรณ์ และสิ่งแวดล้อม ทำให้ยากต่อการควบคุมอัตราการทำความเย็นและความสม่ำเสมอของชิ้นงาน ส่งผลให้เกิดการกระจายตัวของความแข็งและโครงสร้างทางโลหะที่ไม่สม่ำเสมอ ซึ่งส่งผลโดยตรงต่อการตัดเฉือนและการอบชุบด้วยความร้อนขั้นสุดท้าย
(3) การตัดเฉือนการตกแต่ง
เพื่อให้เป็นไปตามข้อกำหนดการวางตำแหน่งของการประมวลผลเกียร์ที่มีความแม่นยำสูง เครื่องกลึง CNC จะใช้สำหรับการตกแต่งช่องว่างของเฟือง รูในและหน้าปลายกำหนดตำแหน่งของเฟืองจะได้รับการประมวลผลก่อน จากนั้นจึงประมวลผลหน้าปลายอีกด้านหนึ่งและเส้นผ่านศูนย์กลางภายนอกเสร็จสิ้นพร้อมกัน ไม่เพียงแต่รับประกันความต้องการแนวตั้งของรูในและหน้าสัมผัสการจัดตำแหน่งเท่านั้น แต่ยังช่วยให้แน่ใจว่าการกระจายขนาดของการผลิตฟันเปล่าขนาดใหญ่จะมีขนาดเล็ก ด้วยเหตุนี้ ความแม่นยำของช่องเกียร์จึงได้รับการปรับปรุง และรับประกันคุณภาพการประมวลผลของเฟืองที่ตามมา
มีสามวิธีหลักในการวางตำแหน่งและการจับยึดสำหรับการประมวลผลชิ้นส่วนเพลา:
1. การวางตำแหน่งด้วยรูตรงกลางของชิ้นงาน: ในการประมวลผลของเพลา ความเชื่อมโยงกันของพื้นผิวด้านนอกแต่ละส่วนและส่วนปลายของชิ้นส่วน และความเป็นแนวตั้งของหน้าด้านปลายถึงแกนหมุนเป็นรายการหลักของตำแหน่งร่วมกัน ความแม่นยำ. พื้นฐานการออกแบบของพื้นผิวเหล่านี้โดยทั่วไป ทั้งสองเป็นเส้นกึ่งกลางของเพลา หากใช้รูตรงกลาง 2 รูในการจัดตำแหน่ง จะเป็นไปตามหลักการของจุดอ้างโดยบังเอิญ
2. วงกลมด้านนอกและรูตรงกลางใช้เป็นข้อมูลอ้างอิงตำแหน่ง (หนึ่งแคลมป์และหนึ่งด้านบน): แม้ว่าความแม่นยำในการตั้งศูนย์จะสูง แต่ความแข็งแกร่งนั้นไม่ดี โดยเฉพาะอย่างยิ่งเมื่อประมวลผลชิ้นงานที่หนักกว่า มันไม่เสถียรเพียงพอ และการตัด ปริมาณไม่ควรมากเกินไป ในระหว่างการกลึงหยาบ เพื่อปรับปรุงความแข็งแกร่งของชิ้นส่วน สามารถใช้พื้นผิวด้านนอกของเพลาและรูตรงกลางเป็นข้อมูลอ้างอิงการกำหนดตำแหน่งสำหรับการประมวลผล วิธีการกำหนดตำแหน่งนี้สามารถทนต่อโมเมนต์การตัดขนาดใหญ่ และเป็นวิธีกำหนดตำแหน่งที่ใช้บ่อยที่สุดสำหรับชิ้นส่วนเพลา
3. ใช้พื้นผิวทรงกลมด้านนอกสองอันเป็นการอ้างอิงตำแหน่ง: เมื่อทำการกลึงรูด้านในของเพลากลวง (เช่น: การตัดเฉือนรูในของเทเปอร์มอร์สบนเครื่องมือกล) รูตรงกลางจะไม่สามารถใช้เป็นข้อมูลอ้างอิงตำแหน่งได้ และพื้นผิววงกลมด้านนอกทั้งสองของเพลาสามารถใช้เป็นข้อมูลอ้างอิงตำแหน่งได้ ข้อมูลตำแหน่ง เมื่อชิ้นงานเป็นสปินเดิลของเครื่องมือกล มักใช้สมุดรองรับสองอัน (หมายเลขชุดประกอบ) เป็นข้อมูลระบุตำแหน่ง ซึ่งสามารถรับประกันความโคแอกเซียลของรูเทเปอร์ที่สัมพันธ์กับสมุดรองรับ และขจัดข้อผิดพลาดที่เกิดจากการเยื้องศูนย์ ของตัวเลข
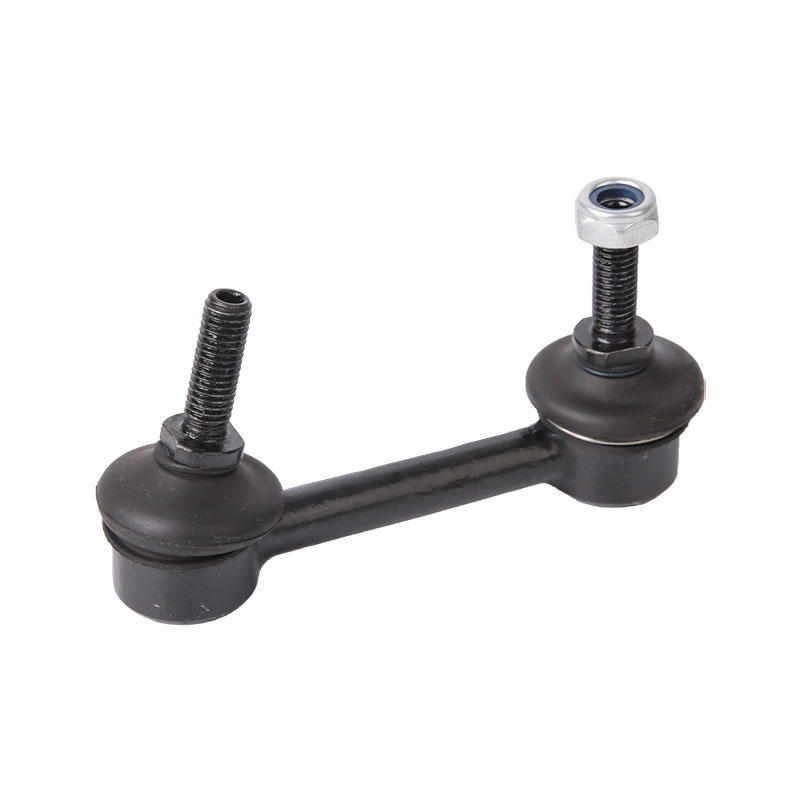
ส่วนที่ II: อะไหล่เชลล์
1. โฟลว์กระบวนการ
การไหลของกระบวนการทั่วไปคือการกัดพื้นผิวข้อต่อ → รูในกระบวนการกลึงและรูเชื่อมต่อ → รูตลับลูกปืนที่คว้านหยาบ → รูตลับลูกปืนที่คว้านละเอียด และการหาตำแหน่งรูพิน → การทำความสะอาด → การตรวจจับการทดสอบการรั่ว
2. วิธีการควบคุม
(1) ตารางการแข่งขัน
กระบวนการตัดเฉือนของตัวเรือนเกียร์เป็นตัวอย่างของ "กระบวนการแมชชีนนิ่งเซ็นเตอร์แนวตั้ง กระบวนการ 10# กระบวนการแมชชีนนิ่งเซ็นเตอร์แนวตั้ง กระบวนการ 20# กระบวนการแมชชีนนิ่งเซ็นเตอร์แนวนอน กระบวนการ 30#" ต้องใช้ชุดจับยึดศูนย์เครื่องจักรกลสามชุดเพื่อหลีกเลี่ยงชิ้นงาน ควรพิจารณาการเสียรูปของแคลมป์ด้วย เช่น การรบกวนของเครื่องมือ การทำงานที่ยืดหยุ่น หลายชิ้นและแคลมป์ตัวเดียว และการสลับอย่างรวดเร็ว
(2) ด้านเครื่องมือ
ในต้นทุนการผลิตชิ้นส่วนรถยนต์ ต้นทุนเครื่องมือคิดเป็น 3% ถึง 5% ของต้นทุนทั้งหมด เครื่องมือประกอบที่มีโครงสร้างแบบแยกส่วนมีลักษณะเฉพาะของความเที่ยงตรงสูง ตัวจับยึดเครื่องมือแบบใช้ซ้ำได้ และสินค้าคงคลังขนาดเล็ก และใช้กันอย่างแพร่หลาย สามารถลดระยะเวลาในการดำเนินการและปรับปรุงประสิทธิภาพแรงงานได้อย่างมาก ดังนั้น เมื่อความต้องการความแม่นยำไม่สูงและเครื่องมือมาตรฐานสามารถบรรลุผลการประมวลผลที่ดีขึ้น ควรใช้เครื่องมือมาตรฐานให้มากที่สุดเพื่อลดสินค้าคงคลังและปรับปรุงความสามารถในการสับเปลี่ยนกัน ในขณะเดียวกัน สำหรับชิ้นส่วนที่ผลิตในปริมาณมาก การใช้เครื่องมือคอมโพสิตที่ไม่ได้มาตรฐานขั้นสูงสำหรับชิ้นส่วนที่ต้องการความแม่นยำสูงสามารถปรับปรุงความแม่นยำในการตัดเฉือนและประสิทธิภาพการผลิตได้